· By Selina M.
Inside the Workshop: The House of Gog Production Process

At House of Gog, we’re driven by a passion for creating exceptional art statues that are not just collectibles, but true works of art. Our process is an intricate, hands-on journey from the initial concept to the final product that ends up in the hands of collectors. Every statue we produce is a result of careful craftsmanship and attention to detail, backed by decades of experience and expertise. Here’s an in-depth look at how we bring our original art statues to life.
An 8 min read, exploring House of Gog’s production process.
The Collector-to-Producer Connection
We take pride in our design team and production workshop, creating a rare and direct link between collectors and producers. House of Gog co-founder Hugues Martel, with his main company Pure Arts, plays a pivotal role in our design and production process. With over 20 years of professional experience in high-quality toy and statue production, Hugues ensures that his unparalleled art direction guides every step.
All of our collectibles are designed and crafted in-house by our team at House of Gog, in our own workshop, with no external production involved. This hands-on approach, enhanced by the incredible expertise and top-tier production pipeline of Pure Arts, ensures that every piece meets our exacting standards, allowing us to produce truly original art statues in limited editions without compromising quality or craftsmanship.
This unique direct connection between creator and collector sets us apart in the industry, making every House of Gog piece personal and authentic.

Selecting the Reference Artwork
The journey begins by selecting the reference artwork we’ll base our statue on. Whether it's a painting, digital art, or another form of artwork, the piece needs to inspire us, fit our vision for a collectible and align with our curation. The artwork serves as the foundation of the entire process, guiding us through every step from design to engineering. We work closely with each artist to capture the essence of the original work so that we can translate it into a physical, three-dimensional sculpture true to the original art.
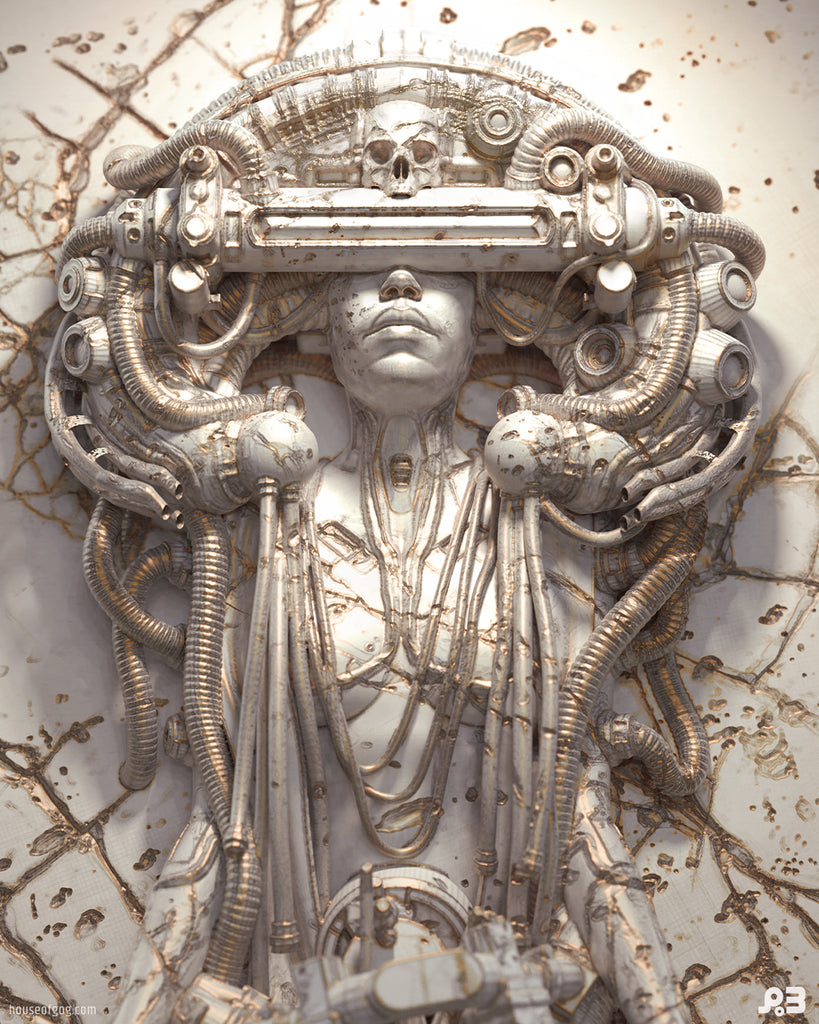

3D Sculpting: Translating Art to Form
Once the reference artwork is selected, the next step is to create a 3D sculpt of the original piece. Using tools like ZBrush, we meticulously craft every detail, ensuring the statue captures the essence of the artwork while adapting it to the requirements of physical production. This step is critical, as we need to ensure that the design is not only faithful to the original but also properly engineered for the production process.
During this phase, we focus on key aspects like separation, ensuring the sculpt is divided into logical pieces that will be cast and assembled later. Proper engineering at this stage helps avoid potential issues down the line as well as to facilitate the paint process for our team.




3D Printing: Bringing the Digital Sculpt to Life
Once the 3D sculpt is perfected, it’s time to bring it into the physical realm. We use a variety of 3D printing machines, choosing the most sophisticated ones based on the complexity and level of detail required for each piece. This stage requires precision to accurately capture every contour, wrinkle and feature, ensuring the printed model mirrors the original artwork as closely as possible.
After the print is complete, we carefully clean each part of the model by hand. This includes removing imperfections like print lines and smoothing out any rough surfaces. This step is crucial to making sure every piece is flawless and ready for the next phase in the process.



The Paint Master: A Blueprint For Precision
Before the molding, we usually create the paint master from our 3D print but since our team handles both the prototyping and the production, we sometime use our first cast instead.
The creation of the paint master prototype for the statue is a meticulous process that establishes the ultimate reference for the entire production run. This prototype serves as the definitive standard, capturing every intricate detail, color and finish envisioned for the final product. Crafted with precision, it undergoes extensive refinement to ensure fidelity to the original artwork.
Once perfected, the paint master becomes the benchmark from which reproductions are made for the limited production run, ensuring consistency and quality in each production unit. This foundational step ensures that every statue produced aligns with our highest standards of craftsmanship and stays true to the prototype.




Molding: Creating the Master Molds
With the 3D prints cleaned and ready, the next stage is to create molds for casting.
We make our molds out of silicone due to its flexibility and ability to capture even the finest details. Silicone molds are ideal for low edition sizes, as they are more affordable than mass production tooling used for larger runs of PVC toys or figures.
However, it’s important to note that silicone molds do degrade after a few hundred casts, so we must replace them periodically. Despite this, the lower cost of silicone molds makes them a more practical choice for producing high-quality, low-edition collectibles.
Once the molds are ready, we begin prepping for the next stage - casting.




Casting: Creating the Final Components
After the molds are ready, we move on to the casting process. This step involves creating the parts for the entire production run, ensuring that each piece is cast accurately and consistently. We pour our high-quality polystone resin blend into the silicone molds to create each part of the statue.
The casting process is carried out with meticulous attention to detail to ensure that every part matches the original sculpt. Each piece is carefully monitored for imperfections and once cast, we inspect each part to confirm its quality and readiness for the next stage. This ensures that the final statue is a true representation of the original artwork and meets our high standards for durability and precision.






Hand Painting: Bringing Each Piece to Life
After casting, each part is meticulously hand-painted by our talented team of painters. This step is where the piece truly transforms into a work of art. The colors are carefully chosen using our own pigments and each layer of paint is applied with precision to capture the intended aesthetic of the original artwork. Since each piece is hand-painted, there are slight variations, making every statue unique.
All painted by hand by our skilled artists, we employ multiple techniques to achieve stunning results, tailored to the specific needs of each piece. These techniques include airbrushing for smooth gradients and base coats, freehand brushwork for intricate detailing and washes to bring out textures and subtle depth. Additionally, we use techniques like dry brushing to highlight raised surfaces, stippling for unique textures and glazing to achieve rich, layered colors.
We pride ourselves on creating some of the most intricate and challenging paint applications in the industry. Each piece is treated as a work of art, combining precision, artistry and passion to deliver unparalleled craftsmanship that brings every detail to life.



Assembly: The Final Touches
Some parts of our statues require assembly, which we perform at our workshop. Parts are assembled using glue and other materials, ensuring that the finished piece is solid and durable. We use magnetic assembly for some sections of the statues, which has multiple advantages:
-It makes assembly easy for collectors, allowing them to build their statue with minimal effort.
-It allows better protection to each piece during shipping, reducing the risk of breakage.
-If a part is damaged during transit or handling, we can replace only the damaged part, rather than the entire statue.
-The magnetic system ensures that the statue remains securely intact without compromising its overall design.





The Art of Authenticity: Hand-Signed Collectibles
At the heart of our dedication to craftsmanship lies a commitment to authenticity. Each of our statues is made even more unique with a genuine, hand-signed artist's signature. To do so, prior to completing production, we send the pedestal sticker - that will be placed underneath the statue - directly to the artist, who personally signs it by hand before returning it to our workshop.
Unlike printed signatures, this process ensures every piece bears the true mark of the artist. This personal touch not only highlights the artist behind each collectible but also elevates its production value and guarantees authenticity.



Quality Assurance: Our Commitment to Excellence
Quality is the cornerstone of everything we do. From selecting the finest artists and reference artworks to perfecting the final packaging of each statue, we are dedicated to upholding the highest standards of craftsmanship. Our quality assurance (QA) process is a multi-step procedure that ensures every statue meets our rigorous standards for detail, durability and overall aesthetic excellence.
Throughout the production process, our team of skilled artisans conducts thorough inspections at each stage - from the 3D sculpting to the hand painting. This includes ensuring that every detail is accurate to the original artwork, that engineering decisions are sound for production and that there are no imperfections in the 3D print. Any issues found are immediately addressed to avoid compromising the final product. Our goal is to ensure that every piece meets the high-quality expectations we’ve set for our collectors.
Our QA team is dedicated to ensuring that each statue is truly a work of art, both in design and in craftsmanship.
We pride ourselves on our attention to detail and our unwavering commitment to quality. The House of Gog production process is built on years of expertise. We want every collector to feel the dedication and skill behind each piece and our rigorous quality assurance measures help us ensure that only the finest statues leave our workshop.


Packaging: Protecting the Art
Packaging is just as important as the statue itself. We design and craft our own packaging in-house to ensure that each statue has not only a cool art box but is also protected during transit. Our custom packaging is designed with care, allowing us to secure each piece in a way that minimizes the risk of damage. With the help of our packaging engineers, we create a safe and aesthetically pleasing package that complements the statue and ensures it arrives at the collector in pristine condition.
While resin can sometimes be damaged during transit, despite our best efforts to ensure its safety, rest assured that our dedicated customer experience team is always here to support you.
At House of Gog, the experience doesn’t end when you complete your purchase - it continues until you’re fully satisfied, with our team always available to ensure you're taken care of every step of the way.


Stress Testing: Ensuring Durability
Before we send out any statues, we perform rigorous stress testing on our packaging to ensure they can withstand the rigors of transportation. This includes drop tests and vibration tests designed to simulate the conditions statues might face during shipping, including the movements and jolts of truck and train transit. These tests help us identify any weak spots in the engineering or packaging, allowing us to make adjustments to enhance the durability of our statues.
Craftsmanship: A Team of Artists and Experts
The entire production process is done by hand in our own workshop - with no 3rd parties involved - and it’s made possible by our incredibly talented team of artists, sculptors, engineers and craftsmen. Many of our team members have decades of experience - some with over 20 to 30 years in creating toys, statues and high-end collectibles. Their skill and dedication to the craft are what make every House of Gog piece so special.

A Collectible Like No Other
We treat every piece as a unique work of art. From the first spark of inspiration to the final brush stroke, every step of our production process is handled with love, care and precision. While the scale of production has evolved, the techniques remain deeply rooted in the spirit of early 1980s garage kits. Instead of traditional sculpting, we now use technologies like cutting-edge digital sculpting and 3D printing, yet, every other step, from intricate detailing to hand-painted finishes, stays true to the craft's origins.
The result is a handmade collectible produced at scale - original art statues that are not only a tribute to the original artwork but also a testament to the passion and skill of the artists and craftsmen behind them.
We invite you to explore our collection and discover the artistry that goes into every House of Gog piece by visiting our website houseofgog.com.
You want to support us? Follow @houseofgog on Instagram, Facebook, X & YouTube
Love ya!
-Selina
Team House of Gog | Community Dev.
"Always the illest for the illests"
